Unlocking the Power of Welding WPS: Strategies for Efficiency and Safety in Fabrication
In the realm of fabrication, Welding Treatment Requirements (WPS) stand as the foundation of welding procedures, determining the needed actions for accomplishing both effectiveness and safety in the fabrication process. Recognizing the complexities of WPS is paramount to utilizing its complete capacity, yet several companies battle to open truth power that lies within these papers (welding WPS). By diving into the approaches that optimize welding WPS, a world of improved productivity and heightened security awaits those going to discover the nuances of this crucial element of construction

Relevance of Welding WPS
The significance of Welding Procedure Specs (WPS) in the manufacture industry can not be overemphasized. WPS work as a vital roadmap that details the necessary steps to guarantee welds are done regularly and properly. By defining important specifications such as welding processes, materials, joint styles, preheat temperatures, interpass temperature levels, filler steels, and post-weld warm treatment demands, WPS give a standardized strategy to welding that boosts effectiveness, top quality, and safety and security in manufacture procedures.
Adherence to WPS assists in attaining harmony in weld high quality, lowering the possibility of flaws or architectural failures. This standardization additionally helps with compliance with industry laws and codes, ensuring that produced structures meet the required safety standards. In addition, WPS documents enables welders to replicate effective welding treatments, leading to regular outcomes throughout different tasks.
Fundamentally, the careful development and stringent adherence to Welding Treatment Specifications are vital for promoting the stability of bonded frameworks, protecting versus potential hazards, and promoting the reputation of fabrication firms for delivering high-grade products and solutions.
Crucial Element of Welding WPS

Enhancing Effectiveness With WPS
When optimizing welding operations, leveraging the key aspects described in Welding Treatment Requirements (WPS) becomes crucial for simplifying procedures and making the most of efficiency. One way to boost effectiveness with WPS is by meticulously picking the ideal welding criteria. By adhering to the specific standards supplied in the WPS, welders can make sure that the welding devices is set up properly, causing regular and premium welds. Furthermore, adhering to the pre-approved welding see sequences detailed in the WPS can significantly decrease the moment invested on each weld, inevitably raising total efficiency.
In addition, correct training and certification of welders in understanding and implementing WPS can further enhance performance. Ensuring that all employee are fluent in translating and carrying out the WPS accurately can rework and lessen mistakes, saving both time and resources. Regularly evaluating click reference and upgrading the WPS to integrate any lessons discovered or technological developments can additionally add to efficiency improvements in welding operations. By welcoming the standards stated in the WPS and constantly seeking means to optimize procedures, makers can attain higher effectiveness levels and premium end results.
Ensuring Safety in Manufacture
:max_bytes(150000):strip_icc()/MIG20welding20arc20in20action-2000-e8844d72f5094d408b5ab6f1c9436a4f.jpg)
Guaranteeing security in manufacture includes a complex strategy that includes different aspects of the welding process. Welders have to be geared up with appropriate gear such as headgears, gloves, and safety garments to minimize threats linked with welding activities.
Additionally, adherence to correct air flow and fume extraction systems is critical in keeping a healthy and balanced workplace. Welding fumes consist of hazardous substances that, if breathed in, can present major wellness threats. Implementing reliable air flow actions assists to decrease direct exposure to these hazardous fumes, promoting respiratory system health and wellness amongst workers.
Routine devices maintenance and evaluations are also essential for making certain security in construction. Malfunctioning machinery can lead to crashes and injuries, highlighting the significance of prompt fixings and routine checks. By prioritizing safety and security actions and fostering a society of awareness, fabrication facilities can produce a productive and safe work atmosphere for their personnel.
Implementing WPS Ideal Practices
To enhance functional effectiveness and make certain high quality outcomes in fabrication processes, integrating Welding Procedure Requirements (WPS) finest methods is critical. Choosing the suitable welding process, filler product, and preheat temperature specified in the WPS is essential for accomplishing the wanted weld high quality. Making certain that certified welders with the needed accreditations lug out the welding procedures according to the WPS guidelines is necessary for consistency and dependability.
Conclusion
In conclusion, welding WPS plays an essential duty in making sure effectiveness and security in fabrication procedures. By concentrating on crucial elements, boosting performance, and carrying out finest practices, firms can enhance their welding operations. It is necessary to prioritize security procedures to stop mishaps and guarantee a smooth manufacturing process. By adhering to these approaches, services can open the complete potential of welding WPS in their fabrication operations.
In the world of fabrication, Welding Procedure Requirements (WPS) stand as the backbone of welding procedures, dictating the essential steps for accomplishing both performance and safety and security in the fabrication procedure. By specifying crucial parameters such as welding procedures, products, joint designs, preheat temperature levels, interpass temperature levels, filler metals, and post-weld heat therapy requirements, WPS supply a standardized method to welding that boosts efficiency, quality, and safety in fabrication procedures.
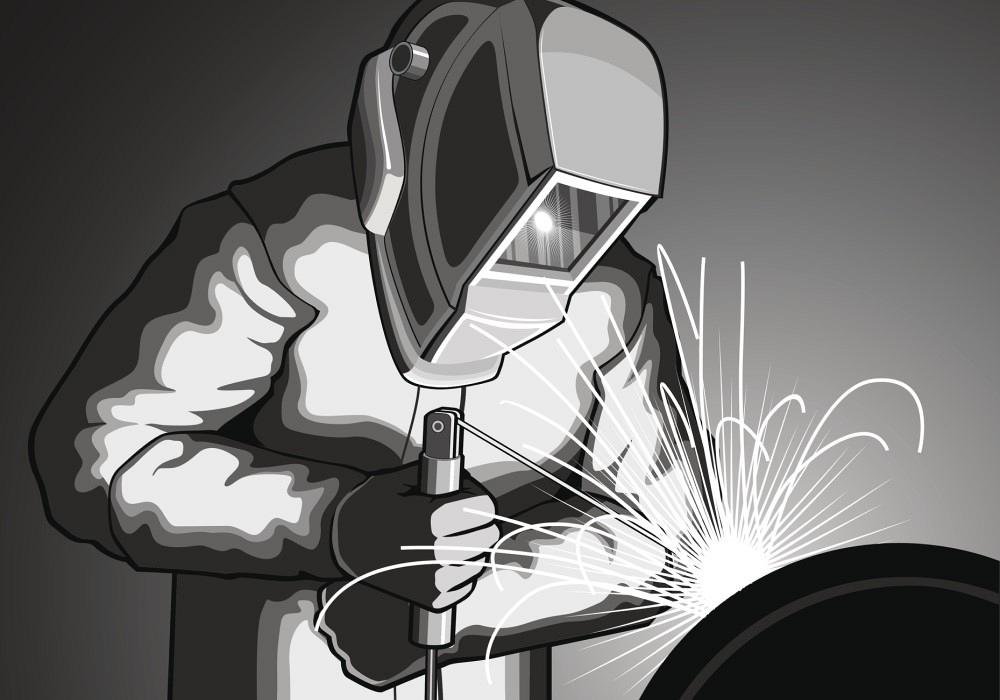
When enhancing welding procedures, leveraging the essential components laid out in Welding Treatment Specs (WPS) ends up being vital for making the most of and simplifying processes performance. (welding WPS)